Casting
Metal injection molding, or die casting, is a metal casting process in which molten metal is pressed under high pressure into a mold cavity. The mold cavity is formed using two hardened tool steel dies, which are shaped and machined in a similar manner as an injection mold during the process. Most die castings are made from non-ferrous metal, especially zinc, copper, aluminum, magnesium, lead, tin and tin-based alloys. Depending on the type of metal used, either a hot chamber machine or a cold chamber machine is used. Aluminum, zamak (an alloy of zinc and aluminum), brass, magnesium and lead are the most commonly used metals and alloys in metal injection molding.
The Foundry, where the casting process is carried out, is the place where high quality products are obtained after the melted and liquid metals are poured into a mold of the desired shape and cooled.
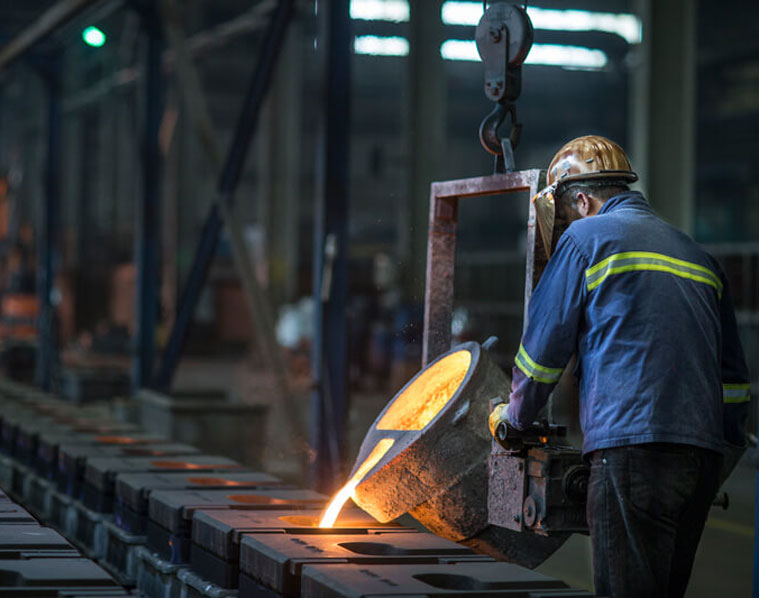
High Pressure Die Casting
The High Pressure Die Casting method, which is the most preferred method in the production of aluminum parts, provides both a price advantage for high quantity production (mass production) and allows even complex shaped products to be produced with high quality.